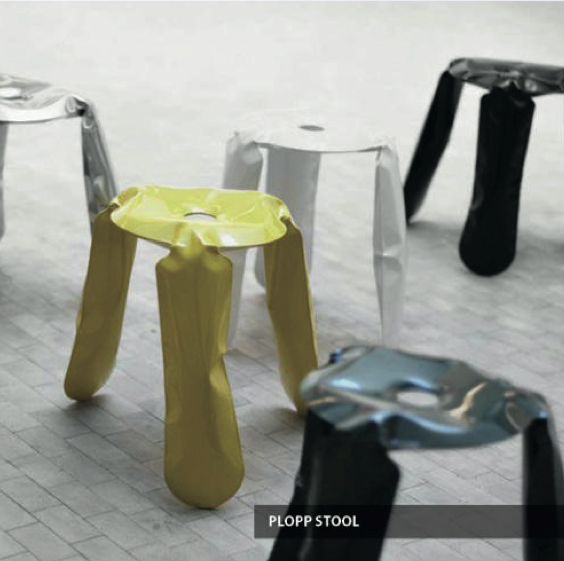
INTERVIEW WITH OSKAR ZIETA – POLITIKA DAILY NEWSPAPER
THE HOCUS – POCUS INNOVATOR
The architect Oskar Zieta is best known for his revolutionary techniques of using metal for the production of more or less everything, from glasses and chairs to facades and bridges.
Oskar Zieta was at the right place on June 6. to 8. “Innovation Squared” – the topic of this year’s three-day Belgrade Design Week conference – is more than fitting for this famous Swiss / Polish designer. He came to Belgrade to present what he is best known for – a revolutionary technique for using metal for the production of more or less everything, from glasses and chairs to facades and bridges. He invented the “FiDU” technology almost a decade ago, and it has become his trademark.
Zieta jokingly calls his production process „hokus pokus“
The products are made with the power of light and air. The term „FiDU“ stands for Free Internal Pressure (Druck) Forming (Umformung). In other words, this is what happens: the metal is laser cut into a desired shape, and that is how, for instance, the front and back of a chair is formed. Parts are easily connected on the edges, also with laser, no matter how curved or sharp-cornered they are, and in the end, the air – sometimes hot, sometimes cold, depending on the results I want to achieve – it is pumped inside through a small hole. The forms are amorphous, the product is light and durable, very firm. The products are made of stainless steel, iron, copper…
Zieta graduated in architecture at the Szczecin University of Technology in Poland, completed graduate studies in 2001 and worked on architectural design using computer-aided technology. He has been associate, researcher and assistant professor at the Swiss Institute of Technology since 2003. His artifacts are part of permanent collections at the “Centre Pompidou” in Paris, the Modern Pinakothek in Munich, the Museum in Zürich and the State Museum in Karlsruhe. The basic model of the “Plopp” chair, on which we were sitting while talking to Zieta for our daily newsletter, became a best-seller, winning the “Red Dot” award in 2008. This chair – which at first glance resembles a toy – is really comfortable and stable, even though it is constructed without a single nail.
“The chair you are sitting on can hold up to two and a half tons – which people find hard to believe. This is exactly the reason why the parts we produce can be used in the kitchen, transformed into a bridge over a river, and even be used in space technology. it is one of the projects i’m currently working on. That’s what innovations are for: that after getting to the Moon, we can reach Mars.”
„Zieta Processdesign”, the company he founded in Swidzerland and Poland, is interdisciplinary. Not surprisingly, it employs artists, architects, designers, engineers, constructors, assistants. Somewhat unexpectedly, a psychologist and a sociologist are also an integral part of the team.
“Everything matters, even the things people might not consider important. For instance, a psychologist can help the team a great deal, especially in discussions we have when we start a new project. It is good to have someone competent in the field of psychology. They get the best of us. Believe me, a conversation moderated by experts is completely different from the one in which they doesn’t participate. in my company everyone works in an interdisciplinary manner – we are truly dedicated to research in the field of ideas and production.”
Trackback from your site.